金属粉末的粒度和粒形表征
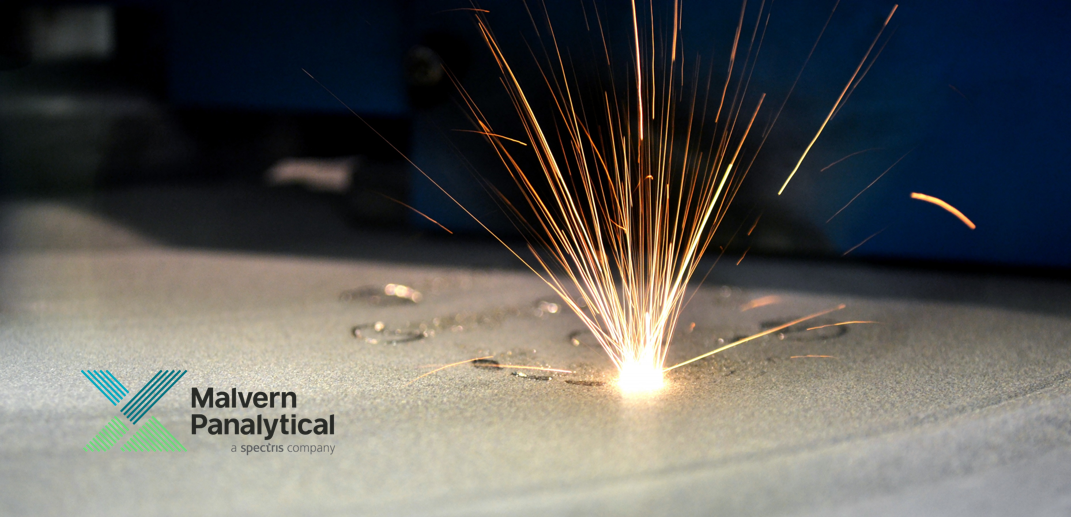
全自动静态图像分析技术
粉末球形度——真正了解与最终成型的零件质量密切相关的金属粉的颗粒形态
叠层增材制造技术相比于传统的减材制造具有很多的优点,但还是存在一些技术难点。例如,在选区激光熔化(SLM)工艺中如何有效的控制粉体床中的金属粉末的质量。金属粉的颗粒形态是重要的材料参数,与最终成型的零件质量有密切关系[1]。
目前,表征颗粒形态的技术有动态图像分析和扫描电镜。动态图像分析技术可测量的颗粒数量大,但是分辨率较低,扫描电镜分辨率高,但是可测量的颗粒数量小。
马尔文帕纳科全自动静态图像分析技术,兼具了图像分辨率高和统计学效果好的优点,通过粒度和粒形的结果成功区分并得到球形度高,球形度较高、卫星粉、延长度高和团聚颗粒的比例。
[增材制造行业趋势?]
以3D打印为例的增材制造工艺可以用较少的原材料生产出复杂的形状,金属部件传统的制造方式一般都是减材工艺,即将一整块金属通过研磨工艺机械制成,那么为什么大家现在对增材技术如此感兴趣呢:
更少的原材料损耗,相比于传统的机械加工,可以节省至多25倍的原材料;
提高了设计的自由度和零件的轻质化,从而提高了航空领域的燃烧效率;
可以制备类似内部管道的具备复杂结构并功能独特的部件;
短的产品生产周期,低的库存量;
可以生产客户定制化的小量部件。
未来四年,增材制造有一个很强劲的增长,每年均增长22.5%,预估到2024年估值达到360亿美金[1]。
[增材制造工艺的难点在哪儿?]
对于增材制造工艺,仍然有一些技术挑战会带来阻碍。比如在选择性激光熔融(SLM)技术中的粉末床工艺中的金属粉末质量问题。图1展示了SLM工艺中金属粉末床如何形成和扫描激光金属形成2D形貌。持续不断的新的粉末床为最终的3D金属部件提供原材料。金属部件的结构一致性和完成件的表面平整度与粉末的化学特性和堆积密度息息相关[2]。
图1 叠层增材制造工艺的粉末床工艺图
图2是粉末床在与激光接触时的熔融池的模拟图像[3],熔融池的温度与粉末的组分和由堆积密度控制的熔池的连续性直接相关,表面模拟图像显示低的堆积密度会导致不连续性。在这案例中,完成件的表面比较粗糙且有可能导致结构一致性的降低。反之,高的堆积密度粉末床会形成一个连续的熔融池,从而生产出表面光滑的结构稳固的完成件。
图2 积密度影响的熔融池分析[3]
粉末的堆积密度是由颗粒大小和形状控制的,从图三可以看出,与多分布粒度相比较,单分布粒度的粉体堆积密度较低[4]。图3也显示堆积密度在中间孔隙被小颗粒填充的情况下达到最大。
图3 堆积密度和颗粒大小的关系
然而,越小的颗粒相比于大颗粒比表面越大,所以粘性越大[5]。这将对颗粒的流动性产生不利的影响。如果粉末不流动,它将不能形成均一和高堆积的粉末床,因此高流动的分布也是很需要的。与粒度类似,颗粒形状也会影响堆积密度和粉末流动性,不规则的颗粒形状和表面摩擦会造成粉末床质量的降低(图4)[6]。
图4 堆积密度与相对的颗粒圆度值
一般而言,叠层增材制造倾向于用圆形金属颗粒,不同的技术所需的颗粒范围不同,选择性激光熔融需要的颗粒大小在15-45um,电子束熔融则需要45-106um的颗粒。因此,用于测试粒度和粒形的技术对质量控制非常有用,但挑战依然存在,因为为了更好的利用原材料,粉末常常被循环利用来构建下一层。这样做的风险在于不断构建材料的质量下降从而导致了部件的失败。对于构建时间在2-5天的制造工艺,浪费成本是很高的,这会大大损害产品产量的增加。粉末重复利用的实效模式尚不清楚,而且不用的工艺实效行为也不同。尽管如此,粉末床的质量和粉体的形貌常常被点到,那么如何表征呢?
用于表征颗粒形貌的测试技术
在增材制造领域,用于测试颗粒大小和形貌的技术主要有三种:动态成像技术,静态成像技术和扫面电子显微镜(SEM)。区别这些技术最简单的方式就是比较采集的颗粒数目和图像的分辨率[8]:
动态图像技术能够提供最多的颗粒数目,但图像质量比较差,所以获取不了好的小颗粒形貌和区分颗粒表面织构;
SEM提供最高的分辨率和小颗粒表面形态细节,但颗粒数目不多,因而只能作为定性技术;
在中间的自动静态技术,是兼顾分辨率和颗粒数目的一个平衡技术,既能用于定性描述,也可以用于定量控制。
图5 M4的内部构造图
实验与结果
在本次研究中,三个金属粉末样品的粒径和粒形被用来分析。第一个是未被使用过的原始样品,第二个是使用了八次的样品,第三个是使用了十六次的样品。均用M4这项自动静态技术,每个样品颗粒数达到100000颗已提供高质量的粒径粒形描述。图5是M4的内部构造图,包含一个校准光栅,自动化的X,Y,Z平台,一组镜头和集成的干法分散单元(SDU)。M4可提供全自动的一整套SOP功能以确保测试结果的准确性和可重复性。
每个样品采集5立方毫米,使用高能自动分散,采用20倍镜头测试和锐利边缘算法。图6显示了三个样品的D10,D50,D90的数量分布图。
图6 三只样品的圆当量粒度分布图,红色是原始粉末,蓝色为使用八次的粉末,黑色为十六次的粉末
三只样品粒度的中位值都在13um左右,小颗粒端有小于1um的颗粒。明显不同之处在于原始粉末的小颗粒比例明显高于使用了八次和十六次的粉末。小颗粒比例的降低似乎是循环使用的结果。小颗粒减少有助于粉体的流动性,然而堆积密度也会降低[9].
进一步的颗粒图片研究发现样品之间的形状差异很大,综合利用颗粒的不同参数,图7给出了不同形状参数的分类图示。例如,任何高灵敏圆度值大于等于0.993并且延长度值小于0.2的颗粒被定义为高圆度颗粒。类似的,高灵敏圆度,延长度值和填实度被用来描述是否有卫星颗粒等等信息。
图7 颗粒分类和相应的颗粒示意图
每个类别的颗粒百分比都可以放在数据的多记录窗口比较[图8],红色为原始粉体结果,绿色为使用的八次的粉体结果,蓝色为使用了十六次的粉体结果。
图8 数量分布的分级图
这三只样品,70%的颗粒都是圆形或者高度圆形的颗。大约13%的颗粒为卫星颗粒,剩余17%的颗粒在形状上颇为不规则,要么显示为长条形或者团聚形。后两种形状的(卫星和不规则颗粒)颗粒的流动性和堆积密度会降低,因而会影响3D器件的质量。然而,针对未使用和使用了八次和十六次的粉体并没有在形状上表现出明显的差异,结果表明使用了十六次的粉体仍然可以使用。
结论
使用次数越多,增材制造的实效成本就会越高。粉末床的质量对部件质量控制尤为重要,而粉末床的质量是由金属粉体的颗粒大小和形貌所控制的。通过表征这些特征,就可能预测出什么时候部件出现问题,从而可以提前避免这一损失。自动静态成像技术是一个可以提供完全表征出多达10000个颗粒高质量粒径粒形结果的解决方案,与动态成像和SEM相比,静态成像技术同时兼顾了定性和定量的控制。
参考文献:
1.https://wohlersassociates.com/2019report.htm.Accessed April 2020
2.https://www.malvernpanalytical.com/en/learn/events-and-training/webinars/W191022Additive. Accessed April 2020
3. Y.S. Lee and W. Zhang, Mesoscopic simulation of heat transfer and fluid flow in laser powder bed additive manufacturing, 26th Solid Freeform Fabrication Symposium, Austin, Texas, 2015
4. J.P. Bennett & J.D. Smith, Fundamentals of Refractory Technology (Ceramic Transaction Series), Volume 25, 2001
(American Chemical Society)
5. C.N. Davies, Aerosol Science, Academic Press, London and New York, 1966
6. DF. Heaney, Handbook of metal injection molding, Woodhead Publishing, 2012
7. J. Dunkley, Metal Powder Atomisation Methods for Modern Manufacturing, Johnson Matthey Technol. Rev., 2019, 63, (3)
8.https://www.malvernpanalytical.com/en/learn/knowledge- center/whitepapers/WP1803278ReasonsAnalyticalImagingIsBetter.html. Accessed April 2020
9. L. Cordova, M. Campos, T. Tinga, Revealing the Effects of Powder Reuse for Selective Laser Melting by Powder Characterization, JOM, Vol. 71, No. 3, 2019